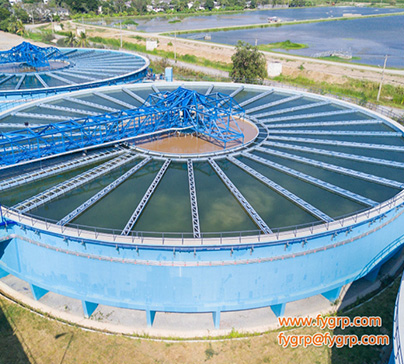
Desulfurization tower
Desulfurization tower
FYGRP professionally design and manufacture of FRP desulfurization tower, Including limestone slurry method, double alkali, magnesium oxide, ammonia and other desulfurization processes, meet the emission standard of below 30 mg/m3 of sulphur content and 5 mg/m3 of dust content. Spray banks can choose 3-5 layers, temperature resistance is 150℃. The mist eliminator can choose the type of vortex plate, flat plate, tube bundle etc. Flue gas flow rate is recommended less than 2 m/s, it can select Inside and outside circulation of the tower, flue gas distributor, flue gas guide ring, side agitator, clean water spray bank, oxidation air pipe, etc. Please provide detailed flue gas parameters and emission standards, FYGRP provides you particular design and construction requirements and meet environmental requirements. Please provide local natural condition data and process data, including wind speed, earthquake grade, rain and snow, maximum and minimum temperatures etc, Through reasonable design, the inner liner of abrasion resistance of tower is 5 mm thickness, The thickness of reinforced layer is designed according to actual situation, The outer surface is coated with anti-aging resin gel to ensure not to fade for ten years. In the year of 2010, after completion of Hebei Yuanda Project, our FRP desulfurization tower didn’t any leak after working at 240℃ for half an hour, using up to now, it was recognized by the user. Please provide the sulfur content, waste gas treatment capacity, dust content, emission temperature, required environmental standards, engineers of FYGRP will provide the most reasonable construction plan and turnkey project.
Please contact tc@fygrp.com for more information.
New technology of stack tower integration
New Technology for the Integration of Smoke Tower into One
Using FRP flue, the flue gas after desulphurization and electrostatic dust removal does not need to be reheated above dew point. FRP flue can save investment and is an economic choice. More importantly, stack tower integration technology can raise height of net flue gas after desulphurization and reduce pollution. It is an inevitable development direction of thermal power plants in the future in domestic.
1. Specification: DN10-25000.
2. Temperature resistance: below 220℃
The "stack tower integration" means that the exhaust gas of power plant is no longer directly discharged through stack into the air, but through the flue to hyperbolic cooling tower, the flue gas after desulphurization and electrostatic dust removal is discharged at high altitude through flue in the tower, the flue and cooling tower is integrated and constitute the exhaust gas emission system. The reason why the flue is made of FRP composite material in stack tower integration project is that its corrosion resistance and durability are very good and service life is long, saving cost. The service life is up to 30 years, which is consistent with the life cycle of thermal power plant, and avoids the economic loss and trouble of shut-down caused by the replacement of pipe material. The anticorrosion cost of flue is saved. At the same time, FRP pipe weight is light, no support needed, saving this part of the construction costs.
Using FRP composites to make flue in"stack tower integration ", Environmental protection is of great significance. The " stack tower integration " technology is developed by Germany. At present , it is used only in four European countries including Germany. Using cooling towers to exhaust gas, the purifying rate of exhaust gas is 97.5%, especially, the landing concentration of exhaust gas is better than that of stack emission. The stack discharge height is about 300 m, and the cooling tower discharge height is 500 m, The diffusion range of treated exhaust gas increases, carbide landing concentration can be reduced to less than 10 mg/m3. Meanwhile, FRP flue can also reduce power consumption and operating costs of thermal power plant equipment; Eliminating the traditional stack, Saving civil construction costs; Due to with cooling tower steam to remove exhaust gas, saving the blower and equipment cost and fan operation power consumption.
Please contact tc@fygrp.com for details