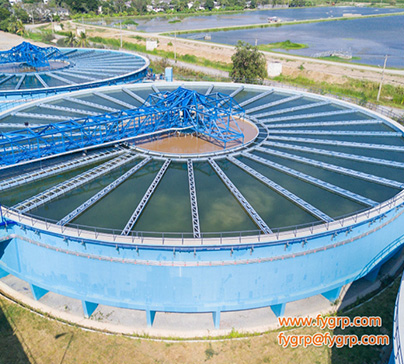
FYGRP ® Tower manufacture process description
FYGRP equipment is manufactured using the latest version of CNC filament winding machine. The specific manufacturing process is as follows:
1.Material selection: we use vinylester resin based on previous experiences, reinforced material is selected E-glass continuous roving.
2. Preparation process
(1)Read the design instructions carefully, pay attention to key issues such as raw material selection, the size of each part, mould selection and lamination design.
(2)Equipment debugging. First, carefully check whether the operation of equipment and working parts are normal, especially whether the resin-curing agent two-component pump is clogged, and whether the ratio meets the design requirement, ensure the stable operation and work accuracy of the equipment such as making inner liner, winding, trimming, demoulding, etc.
(3) Clean mould. The mould surface is required to be free of pits, dust, debris and other attachments. The mould surface should be smooth. If there is a problem, repair and maintain in time.
(4) Wrap polyester film. In order to facilitate demoulding, a layer of polyester film should be coated on surface of the mold. The overlap width of film is 1~2cm and the thickness is about 40um. It is required that the film has no damage, no wrinkles, and both sides are smooth and clean. The film quality meets requirements of GB13950-1992.
3. Body inner liner forming. The inner liner is divided into inner layer and transition layer according to the structure. This layer mainly plays a role of corrosion resistance and impermeability.
(1) Inner liner resin preparation. Inner liner resin is mixed by quality inspection department according to resin formula system made base on working environment and temperature at that time, the amount of ingredients should be reasonably controlled according to manufacturing schedule. When the situation changes on-site, the manufacturing department should adjust the formula in time and prepare appropriate resin according to the new formula.
(2) Making inner liner according to design lamination sequence. Adopts steel mould, forming by Venus spray gun. The inner liner resin content is high and has good effect of anti-corrosion and anti-seepage. The resin content of inner liner is 90+2%, and of the transition layer is 80%.
(3) Process inspection. After applying every layer as per design requirement, the operator is required to conduct preliminary quality inspection, whether the inner liner reaches design thickness, whether there is poor glue or hanging in local area, whether there are white spots or bubbles, if so, it should be reported and taken treatment measures immediately.
(4) The inner lining is deeply cured and demould.
4. The upper and lower heads are forming and reinforced. The head is divided into inner liner and structural layer as per structure.
(1) The forming process and raw materials of inner liner of heads are the same as that of body. Spray forming by spray gun, resin content is high. After inner liner of head applying completed, deeply curing.
(2) Apply head structural layer, spraying roving and woven roving alternately. Each single layer of woven roving should be applied with proper tension during laying process, overlap with each other properly, and drive out bubbles with combined roller repeatedly rolling to ensure the fiberglass is completely permeated with resin. Each reinforced layer is required to reach the design resin content.
(3) Process inspection, deep curing, demoulding.
5. Assembly
(1) The cured inner liner of body and head are demoulded and cut to the size specified in the design document.
(2) Body inner liner is butt joint with head using assembly ring,adjust the assembly ring to the nominal diameter of Φ-30mm, insert the assembly ring into body inner liner, expand the assembly ring to nominal diameter of Φ-15mm, and put the lower head on the exposed part of assembly ring, slowly expand the assembly ring, and measure the circumference of inner liner and the diameter at 3 points (uniformly distributed) till meet standard requirement.
(3) Apply outer reinforced layer of butt joint, grind the joint area, apply the outer joint by stair type (width increasing) from inside to outside. The width of the outermost layer is not less than 500mm. After the overall reinforcement is completed, bond inside seam with inner liner resin and chopped strand mat,laminate by stair type(width increasing) from outside to inside.
(4) Procedure inspection.
6. Overall reinforcement
(1) Connect the assembled equipment shell to the numerical control fiber winding machine, grind and trim shell outer surface. Drill at the nozzle of inner liner, inflate to ensure the roundness of inner liner.
(2)Reinforce locally the stress concentration area of lower head and body knuckle with chopped strand mats. Adjust winding angle and head wrap angle to adapt the stress concentration characteristics of the head. The wrapping width of the lower head is more than 250mm and the wrapping height of body is 400mm.
(3)Adopt one high and three many, back winding and forward spray. Spray roving, hoop and cross winding alternately, adjust the rotating speed of inner liner and fiber tension to ensure the resin content of tank wall. The bottom surface of lower head of equipment with outer sloping bottom is not perpendicular to the axis of the equipment, adjust the winding equipment and winding parameters, the cross-winding length in overall reinforcement is greater than the length of equipment body, the winding roving forms flower bud wrapping on the upper and lower heads of equipment.
(4)Procedure inspection, deeply curing.
7. Assembly nozzles. Mark position, opening and install nozzles according to drawings.
8. Outer protective layer. After overall production is completed (including accessories installation), coat protective layer, anti-aging gel coat resin with ultraviolet absorbent and toughening agent.
9 Deliver to inspection.