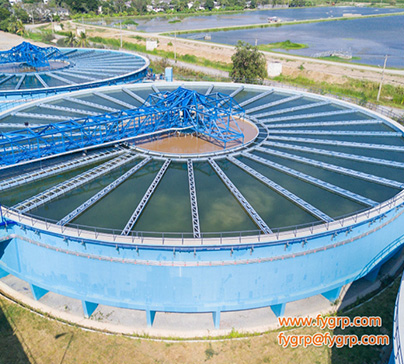
Production process description of PVC/FRP storage tank
The PVC/FRP equipment is manufactured using the latest version of CNC filament winding machine by FYGRP. The specific manufacturing process is as follows:
1、Read the design instructions carefully, pay attention to key issues such as raw material selection, the size of each part, mould selection and lamination design.
2、Equipment debugging. First, carefully check whether the operation of equipment and working parts are normal, especially whether the resin-curing agent two-component pump is clogged, and whether the ratio meets the design requirement, ensure the stable operation and work accuracy of the equipment such as making inner liner, winding, trimming, demoulding, etc.
3、Grind the surface of PVC cylinder. The mold surface is required to be free of pits, dust, debris and other attachments. The mold must be made smooth and repaired and maintained in time if there is a problem.
4、Make the middle layer. After the PVC cylinder is ground, apply a layer of chopped strand mat on surface of cylinder with A410-901, special adhesive for PVC and FRP, by hand lay-up.
5、Overall reinforcement
(1) Connect the assembled equipment shell to the numerical control fiber winding machine, grind and trim shell outer surface.
(2)Reinforce locally the stress concentration area of lower head and body knuckle with chopped strand mats. Adjust winding angle and head wrap angle to adapt the stress concentration characteristics of the head. The wrapping width of the lower head is more than 250mm and the wrapping height of body is 400mm.
(3)Adopt one high and three more, back winding and forward spray. Spray roving, hoop and cross winding alternately, adjust the rotating speed of inner liner and fiber tension to ensure the resin content of tank wall. The bottom surface of lower head of equipment with outer sloping bottom is not perpendicular to the axis of the equipment, adjust the winding equipment and winding parameters, the cross-winding length in overall reinforcement is greater than the length of equipment body, the winding roving forms flower bud wrapping on the upper and lower heads of equipment.
(4)Procedure inspection, deeply curing
6、Assembly nozzles. Mark position, opening and install nozzles according to drawings.
7、Outer protective layer. After overall production is completed (including accessories installation), coat protective layer, anti-aging gel coat resin with ultraviolet absorbent and toughening agent.
8、If it is a tower body, after the whole winding is completed, it is disconnected according to the size of the tower section, and the PVC cylinder flange is welded to strengthen separately.
9、Submit for inspection