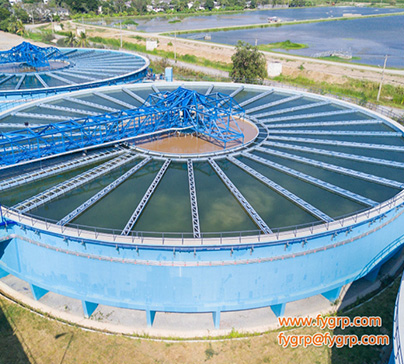
The description of FRP equipment manufacturing process in chlor-alkali industry
The chlor-alkali industry is the high corrosive industry. Materials used to manufacture this kind of equipment must be resistant to corrosive media such as caustic soda, ammonia, hydrochloric acid, backwash brine, and sodium hypochlorite etc. The correct selection of corrosion-resistant materials is prerequisite for controlling corrosion and prolonging service life. It is also an arduous task. Our company has analyzed and summarized the equipment previously made for the chlor-alkali industry, and learned requirements of the production process and media on the equipment. FYGRP can produce corrosion-resistant FRP products for customers through selection of resin types and brand, and appropriate forming processes, based on the principle of advanced, applicable and economical.
(1)、FRP application in production equipment of chlor-alkali industry
1、Brine refining stage
The crude brine after original salt dissolution contains impurities such as Ca2+, Mg2+, SO42-, Fe3+ and can not be directly used in the electrolytic cell, and control the precipitation of Ca2+, Mg2+, Fe3+ ions in refined FRP equipment to control its content.
According to the control requirements of FRP equipment, in the manufacturing process, the inner liner anticorrosive layer is usually double-inner liner, and polyester fiber as reinforced material, low Ca2+, Mg2+ resin is used as base material to reinforce FRP products. Generally, the resin type is Vinyl ester.
2、Electrolysis stage
Due to brine electrolysis includes corrosive media such as sodium chloride solution, wet chlorine, ammonia, dilute brine, hypochlorous acid etc., it has higher requirement for selection of materials for equipment and piping in production facilities.
FRP equipment used in this stage includes: chlorine water seal tank, trap, chlorine water storage tank, chlorine scrubber, water mist separator, high-purity hydrochloric acid storage tank, hydrochloric acid storage tank, etc. The separator adopts PVC/ FRP structure, others can adopt FRP structure.
3、Chlorine treatment stage
The process of chlorine treatment approximately includes chlorine cooling, drying and dehydration, purification and compression and transportation. The main corrosive media are wet chlorine, ammonia and dilute sulfuric acid. In this section, FRP equipments include: dechlorination tower, packing drying tower, chlorine absorption tower (also called bubble cap drying tower), etc., generally adopt PVC/FRP structure.
4、Chlorine and wastewater treatment stage
The low-purity chlorine produced when the electrolysis project is started and stopped, the accidental chlorine gas and the waste chlorine and hydrochloric acid gas produced by every process are all treated in this section. Use low-concentration alkali to absorb to generate sodium hypochlorite solution which has extremely corrosivity when it is unstable. Originally, adopt PVC as inner liner and FRP as reinforcement layer. However, our company adopts the full FRP structure using the latest imported vinyl ester resin.
5、In the above stages, pipes that are matched with equipment and meet the process can adopt PVC/FRP structure.
In view of the application of above FRP products in the chlor-alkali industry, each stage of every equipment such as selection material, design, manufacturing and inspection etc. strictly follows international quality system of ISO9001 from raw material inspection, product design and manufacture to quality inspection and after-sales service and other procedures. FYGRP manufactures high-quality products that meet user operating and quality requirement .
(2)、About raw materials selection
With the rapid development of the chemical industry today, many vinylester resins of good performance have emerged, and they can be used as inner liner material replacing many PVC.
FRP is glass fiber reinforced plastic, which is composed of matrix material-resin and reinforced material-fiber.
Matrix material—resin are mostly synthetic resins. Vinyl ester resin is the most widely used in the chlor-alkali industry. Derakane-470 resin has excellent comprehensive performance of corrosion-resistance and resist some solvents and oxidant media. Its heat deformation temperature reaches 120°C. In addition, PalatalA410-901 has a wide range of applications and high mechanical strength, heat degradation and chemical resistance. It is mainly used as adhesive between polyvinyl chloride (PVC) and glass fiber reinforced plastic (FRP). FYGRP does the test of Shear strength test and the test result reaches 75Kg/cm.
(3)、Manufacturing process and control points
The structure of FRP equipment is lamination type, roughly divided into three layers: Inner liner, structural layer (reinforcement layer) and anti-aging layer.
1、The anti-corrosion layer of inner liner mainly plays the role of corrosion resistance. It is a resin-rich layer with resin content of more than 92%. The choice of matrix material should be based on the working conditions of the equipment and pipelines. The reinforcing material should be selected polyester surface mat based on low Ca2-, Mg2- etc. is required for equipment and pipelines. It is made into double inner liners that play the role of double insurance, which can effectively prevent the precipitation of Ca2+ and Mg2+ ions in reinforcing materials and matrix material.
2、The impermeable layer (secondary inner layer) of inner liner, the base material is the same as above, reinforcement material is selected E-glass spray roving from Zhejiang Jushi Group. The resin content of this layer is 75-80%.
3、Structural layer: This layer is the main bearing layer to ensure that the product has sufficient strength, rigidity and stability. It adopts one-high-three-many (high-strength, multi-point, multi-angle, multi-level) cross-winding automatic forming method, and is produced in strict accordance with the design documents. Control the winding angle. Different winding angles are used for vertical vessels and horizontal vessels to ensure that the strength of equipment in the circumferential and axial directions is reasonably distributed.
The base material used is generally vinyl ester resin, such as DOW411# resin, and the reinforcement material is selected E-glass winding roving from Zhejiang Jushi Group.
4、Anti-aging layer: This layer, a protective layer to prevent the equipment from aging, plays the role of extending service life of the equipment.
The process: add paraffin styrene solution and ultraviolet absorber to the gel coat resin. After the outer protective resin is cured, the paraffin is precipitated, which can effectively isolate the oxidation reaction of oxygen and the matrix material. The ultraviolet absorber can convert ultraviolet light into heat or Secondary radiation, which plays a protective role and prolongs the service life of the equipment. In addition, flame retardant can be added, or flame retarded resin can be used, and its oxygen index can reach 36 or more, which can fully meet the fire protection requirements of users.
Nozzle assembly: Before the vessel is assembled, select the reference point to open hole. For vertical vessels and towers, the bottom plane is the reference point, so that the user will not easily cause misalignment when fitting the process pipe.
PVC/FRP structure equipment, the structure is PVC lining, transition layer (adhesive layer), reinforcement layer, and outer protective layer. The reinforced layer and outer protective layer are similar to the full FRP structure. For the PVC lining layer and transition layer, the manufacturing process is as follows:
The PVC part adopts standard-compliant hard PVC sheets and pipes used in chemical industry. The welding adopts hot-air welding. The weld structure should be uniform and dense without scorching. The manufacturing and acceptance of the PVC shall exert "Technical Conditions for Polyvinyl Chloride Plastic Equipment" CD130A18-85.
The inner and outer surfaces of the cylinder body and the head are smooth, Two ends flanges of tower section is welded with tower body, after that do secondary processing to the sealed surface. After the equipment is welded, the weld seam is checked with 100% electric spark. Make adhesive layer after qualified, first remove the oil on surface of PVC equipment, then grind to the rough surface with grinder, evenly coat surface treatment agent and adhesive (using A410-901 resin), and lay the chopped strand mat completely soaked, laminate1 or 2 layers as per equipment specifications and models The control point is also bonding of this laye.
Regarding the flatness of internal parts such as grid in tower, the flatness tolerance after installation should be +2mm, and that of spray pipe should be +3mm when installing, and other accessories should meet requirements of drawings.
For tower equipment with skirts, after the tower body is manufactured completely (that is, the winding reinforcement layer is manufactured ), measure the outer diameter of the bonding position that the lower part is bonded with skirt, and then weld the skirt, skirt body and bottom pad. Pay attention that nozzles and flanges on equipment interfering with the skirt are welded and strengthened after the equipment and the skirt are installed completely.
Process improvement comprehended with characteristics of chlor-alkali industry:
1、Storage tanks. In the chlor-alkali industry, in the past, Electrolyzers and pure hydrochloric acid tanks used bisphenol A type 3301 resin to make inner anti-corrosive layer. After a period of use, other manufacturers found that the color of hydrochloric acid turned yellow, then discussed with our company. After we studied with resin supplier, we thought the resin itself didn’t exist quality problems and fabrication met the requirement. It might be material selection problem. So, the lining protective resin was changed to vinylester resin due to its good corrosion resistance and chemical stability. After several years of use, it had been proved that the medium in the equipment made with vinylester resin did not change. Equipment that requires low Ca2-, Mg2+ etc. should do post-processing after it is finished. The treatment method is: First wash with detergent and then with fresh water, rinse twice with hot water at 80°C. After drying, the test should reach the required COD value.
The winding angle is controlled 60°for vertical storage tank when making reinforced layer, so that hoop strength is greater than axial strength, and the wall thickness of shell increases with pressurizing (mainly hydrostatic pressure) , showing stair type distribution. Nozzles that diameter is less than DN50 should be reinforced with 4 rib plates when assembling. Discharge port adopts reducing flange. In this way, the bonding strength with tank body and its own strength are higher.
2、Large storage tank winding on site. Our company introduced the foreign site winding equipment and technology and has improved based on that. The introduced site process is hoop winding by computer controlling which had no cross winding due to there was a certain difference between raw materials in domestic and abroad. Thus the structural layer of equipment using this process occurred hoop crack after a period of use. This problem is highlight in chemical industry. So we improved based on hoop winding control procedure, and designed and manufactured site winding machine involving hoop and cross winding procedures. FYGRP does product design and process design according to working conditions of site storage tank. Adopts automatic winding forming method of loop and cross alternately during construction process on-site, meanwhile using roving cloth to ensure quality, provide the hoop strength and axial strength and make site storage tank possess high mechanical strength and stability.
3、Tower
The traditional design for tower is generally PVC/FRP composite structure, because PVC resists corrosion by media such as acid and chlorine etc, especially drying towers and bubble towers. With rapid development of modern chemical industry, the PVC lining of some towers can be replaced by vinyl ester resin. For the chlorine scrubber and chlorine accident treatment tower currently produced, the lining anticorrosive layer uses Ashland D470, so the inner liner has the same material with structural layer and outer protective layer, to avoid the phenomenon of interface peeling due to different thermal expansion coefficients of different types of materials.
The flange face for connecting on tower was not machined in the past, only thickened gaskets to seal, but after a period of use, due to gasket is thicker, the gas erosion rate is faster, resulting the gasket soften. It is easy to leak in the place where the gap of joint surface gap is big. For this reason, our company conducts mechanical processing on the joint surface of all tower flanges to ensure that the gap between two flanges is minimized and the gasket is tightly bonded.
For drying towers made of PVC/FRP composite structure, after welding, in addition to inspect welding seams with 100% electric sparks, do the airtight negative pressure test after overall assembly is completed.
Make reinforcement layer for all towers and pressure vessels. After finishing the inner liner, spray and hoop winding, then cross winding, so as to avoid uneven interlayer stress caused by directly cross-winding due to uneven outer surface of inner liner, rotating ring having deviation and uneven winding tension.
4、Pipe
The lining anti-corrosion layer and flange connection surface should be double-layer structure, and material is the same with the device connecting with it. The outside of pipe protection layer should be polished using polyester film. For chlorine-alkali industry, the surface erosion to chlorine pipe has one more protective layer of protection.
The equipment manufactured by FYGRP is more perfect after we continuously improve and perfect to the process. Some process technology has been praised by Italy. Our technical level has reached international standards.
At the inspection stage after the equipment is manufactured, the quality inspection of equipment and pipelines shall be carried out according to the "Technical Conditions of Polyvinyl Chloride Plastic Products Equipment" CD130A18-85 and "Fiber Reinforced Plastic Storage Tanks" JC/T587-1995. Pack and ship after passing the inspection. The tower should be fixed with saddle before loading, so as to prevent the tower from being damaged by bumps during transportation, resulting quality problems.